Tensioned access platforms are a “floating floor” and an alternative to scaffolding and lifts for work at the ceiling or roof in both renovations and new construction.
It’s a simple enough concept that could have an outsized effect on the efficiency of “at height” projects.
Tensioned access platforms (TAP) are simple yet carefully designed systems made from panels of either net or membrane, tensioned between structural members that can be walked on and worked from as a work platform. Webbing secured to the panels is ratcheted to engineered anchor points, providing tension and stability to the platform. Widely used in the United Kingdom and the Middle East for a variety of projects, TAPs are still largely unknown in the USA. I’ll discuss applications, installation methods, drawbacks, relevant standard regulations and a case study but first a picture is worth a thousand words:
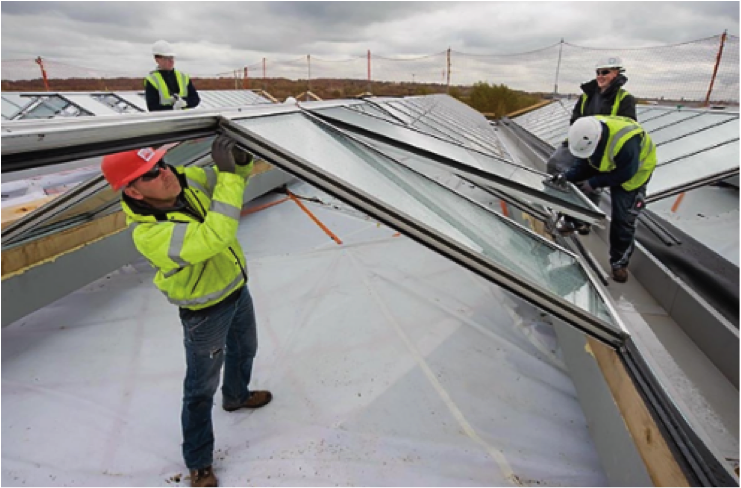
Observe the matrix of webbing beneath the membrane and the worker in the forefront standing on the TAP without fall protection as if it is rigid ground, with little to no deflection. Photo courtesy of SpanSet®.
Applications
Applications for TAPs are wide and varied – from small painting projects to massive stadium roofing installations. The main advantages of TAPs over other approaches – namely pipe frame and suspended scaffolding are: 1) TAPs are a cost effective access system for safe work at height; 2) TAPs are efficiently installed and removed; and 3) TAPs entail minimal disruption to the job site or occupied building.
The glowing example of a TAP system in the USA is the roof installation at the new U.S. Bank Stadium in Minneapolis. The stadium roof is made from ETFE panels, all of which were installed from TAPs located between the steel bays. In this case InCord’s SkyNet product was used. According to the safety director for the General Contractor on that project, a normal bay was 10’x60’ and the TAP was engineered to hold a maximum of six workers and workers were on additional fall protection 100% of the time. The alternative access method in this scenario was to install swing stages at the stadium roof bays. This approach would have significantly increased the time and money required for project completion.
But TAP applications need not be so glamorous or large-scale. According to Andy Traynor of the UK based company Base Structures, TAPs are often used in shopping mall construction. As build outs within the individual shops AND construction of the roof may be occurring simultaneously, scaffolding is impractical, or at the very least schedule crippling. With a TAP system secured to the rafters workers may install the roof while work in the shop spaces continues beneath them. And of course, TAPs can be used when a roof needs to be removed rather than installed. In certain situations, and if it is engineered accordingly, the TAP may double as a debris containment net. When debris containment is required one must be aware of OSHA 1926.451(f)(13), which prohibits debris from accumulating on scaffold platforms. In this case the platform must be made from either an impermeable membrane or a net with a debris liner.
Painting and glazing projects are two typical applications of TAPs. For example, as part of a standard building maintenance program the trusses over a busy train terminal need to be painted but the building cannot afford the disruption scaffolding would create for commuters. In this scenario the TAP system provides an alternative access method in which painting can occur either during working hours (if proper drop clothes are deployed) or at night.
The span of the TAP is determined by two factors: The first is anchor integrity. The second is deflection- if sag is so great that work become difficult it is no longer an efficient system.
Types of structures that may benefit from TAPs are stadiums, shopping malls, train stations, atriums, conservatories, church naves, natatoriums, hangers, power stations, water towers, bridges, offshore drilling rigs and refineries.
Installation Methods
As tensioned access platforms are used for projects at height and since the ratcheting of panels requires some torquing of the worker’s body it is imperative installers are not at risk of any falls. This stipulation then excludes ladders and mobile access towers as an access and installation method.
Where there is proper clearance and solid ground conditions, mechanical lifts (aerial platforms, scissor or boom lifts, etc) are the easiest and most cost effective method. Lifts offer a stable working platform and are ubiquitous. Aside from their main draw back – work is limited to boom height – access using mechanical lifts is a safe and is the most practical method of installation/removal.
For projects out of reach of mechanical lifts, properly trained technicians can install netting in many different situations utilizing industrial rope access. Industrial rope access employs lightweight rigging systems with redundant work positioning and fall protection connections to gain access to otherwise difficult to reach locations. In this system, technicians are always connected to at least two separate points, either directly to structural members or by rope using industry-specified hardware and equipment. As with all access systems, it is important to always have safety considerations in place and clear rescue protocols established.
Drawbacks
For certain projects, especially for projects “at height” involving roofs, it makes a lot of sense to employ tensioned access platforms. But, TAPs are not a silver bullet. There are several drawbacks.
The main drawback is that deflection within the net sometimes makes walking difficult and can be tiresome of workers legs. Depending on net span and tension, according to sag can be as much as 18 inches in the center of net bays. As you move closer to the structural perimeter the sag decreases.
TAPs are often, though not always, used on projects out of the convenient reach of lifts and so require specialized installation procedures, which typically involves contracting out to a rope access company. This may add a layer of complexity to a project, requiring additional coordination.
As TAPs are not widely used in the United States, there will be confusion over OSHA regulations. Does it or does it not comply is a legitimate question that will need to be answered for each project and will always need to be backed by sound engineering.
The last drawback is somewhat abstract. Design and use of TAP systems is an unusual approach and may inspire some confusion and fear of the unknown. There are few workers who are familiar with TAPs and some might be hesitant to work on them, especially at height.
Relevant Standard Regulations
Understanding the potential applications and actual case studies are only one part of the equation. Equally important is the regulatory side, which is not always clear in the instance of a TAP. OSHA currently does not have specific TAP regulations, so the design of each TAP must follow the generalized work platform standards set out in (OSHA 29 CFR 1910.28), which requires the design be completed by a qualified person.
Although TAPs may include netting or a membrane material it is interpreted as a scaffold and so must meet the standards of (1910.28) rather than the standards of a safety net (1926.105). In fact, work position netting is a bit of a misnomer: a TAP is not simply a tensioned safety or personnel net. Any net used in a TAP systems needs to be engineered specifically for the load cases it is designed to support.
The strength component of the panel material must be four times the maximum intended load (§1926.451(a)(1)). Tension webbing and connecting hardware under §1926.451(a)(3) must be six times the maximum intended load and §1926.451(d)(12)(iv) requires pre-shift inspection and if necessary re-tightening of ratchets.
In the unlikely event the TAP is built in such a way to fall under the same category as catenary scaffold, than, under §1926.451(g)(1)(i), all workers must use additional fall protection. Though, likely, even if it does not classify as catenary scaffold, best practice will call for additional fall protection. If no fall protection is being used 1926.451(g)(1)(iv) necessitates a guardrail with a minimum 200 pound top rail capacity near any fall hazards.
In addition to the relevant OSHA regulations, all TAP systems must comply with ANSI Test Methods specified under A10.11- Safety Requirements for Personnel and Debris Nets.
Case Study: Aviva Stadium, Dublin, Ireland
This portion of the article is used with permission from SpanSet. WalkAbout™ is their tensioned access platform product, which consists of membrane panels tensioned by polyester webbing.
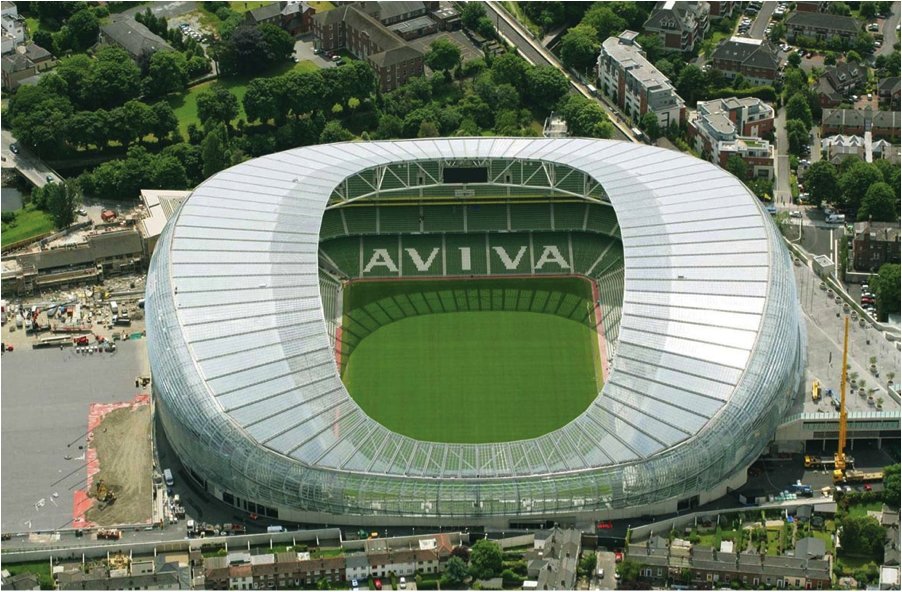
Photo courtesy of SpanSet®
“The original multi-discipline ground was in existence at the Lansdowne Road site since 1872. In its old incarnation, prior to closure in December 2006, it was the oldest rugby union ground worldwide and oldest sports stadium in Europe. The stadium is the home to the Irish national rugby and Republic of Ireland national football team. Aviva Stadium is now Ireland’s only UEFA Category 4 Elite Stadium and has won a number of awards including RIAI and RIBA. The Aviva Stadium in Dublin, built by John Sisk & Son and completed in April 2010. WalkAbout™ was used in the construction of the 19,000 sq.m stadium roof with 4,251 polycarbonate panels.
The roof construction original planed to use a scaffold structure to install the glazing bars and polycarbonate panels. At an early stage of the roof construction the WalkAbout system was trialled alongside the scaffold system to identify if time and cost savings could be made. As a result of these trials the WalkAbout system was adopted as the access method for all the roof construction. The grounds for this decision were the speed at which the system can be installed and dismantled with fewer staff. This gives major savings in both man hours worked at height and reduced cost in both labour and on hire cost.
In addition to the direct benefits the construction also benefited from the increased access now that the scaffold structures were not in place and work could continue at ground level providing further time savings to the project. As a result of the use of WalkAbout the project saved 16 weeks construction time and completed the roof works ahead of schedule.” Read more here.
Please consider this article only a brief introduction to tensioned access platforms. Further questions regarding load limits, longevity, weather resistance, tension calculations and other such questions were left unaddressed.
For more information please contact Walker Diebolt at walker@AltaAccess.com.